Touchscreen technologies explained: PCAP, resistive and SAW touch compared
Everyone has it – touchscreen technology. Touchscreens are ubiquitous these days, whether in the form of smartphones or tablets. But the world of touchscreen technology is much more diverse. Especially in demanding environments, displays need additional features to meet the different application scenarios. In addition to functionality and fast responsiveness, robustness and enhanced usability are critical.
In this blog post, we will focus on the structure, functionality, advantages and disadvantages of different touch technologies in demanding environments. The focus is on PCAP touch, resistive touch, and surface acoustic wave touch.
The different touch technologies in detail
PCAP Touch: The all-rounder
PCAP stands for Projective Capacitive Touch. Most people are more familiar with this technology when it comes to smartphone touchscreens. But how does PCAP touch work?
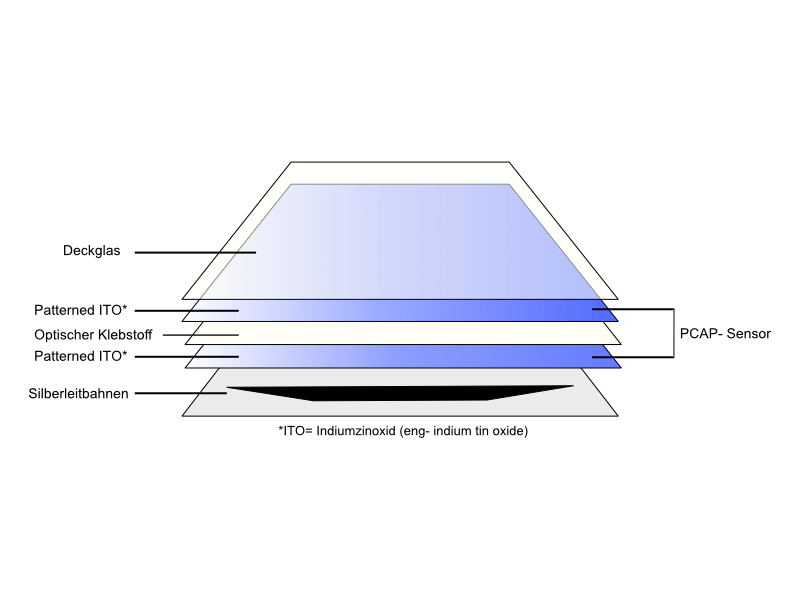
The structure is made up of several layers. The main layer is also called the touch sensor, cover lens, or cover glass. It is made of glass or foil and is directly connected to the touch controller. Touching it with a finger or conductive stylus changes the electrical capacitance on the user surface. Behind the glass is a transparent sensor that detects this change. This information is measured and registered by the integrated controller, which converts the changes into two-dimensional position data (X,Y). This process allows tactile positioning. In addition, the sensor is capable of detecting multiple touch points simultaneously, which is known as the multi-touch effect. This technology makes it possible, for example, to zoom in and out on photos.
In everyday life, this technology is used in smartphones, tablets, etc. PCAP touch can also be found in industrial contexts such as industrial automation, food processing, and medical.
Resistive touch: The pressure-sensitive
Whether you use your finger, a stylus, or a glove, resistive touch responds to pressure, not touch like capacitive touchscreens.
The resistive touch screen consists of two conductive layers that are connected by touch pressure. The bottom layer is usually glass. This layer is energized to determine the exact position of the pressure point via the electrical resistance. The resulting information is sent to the operating system and executed.This technology is used in industrial panel PCs for controlling machines, information terminals or in the automotive sector. However, resistive touchscreens are losing market share. This is mainly due to the evolution of capacitive touch in terms of resistance.
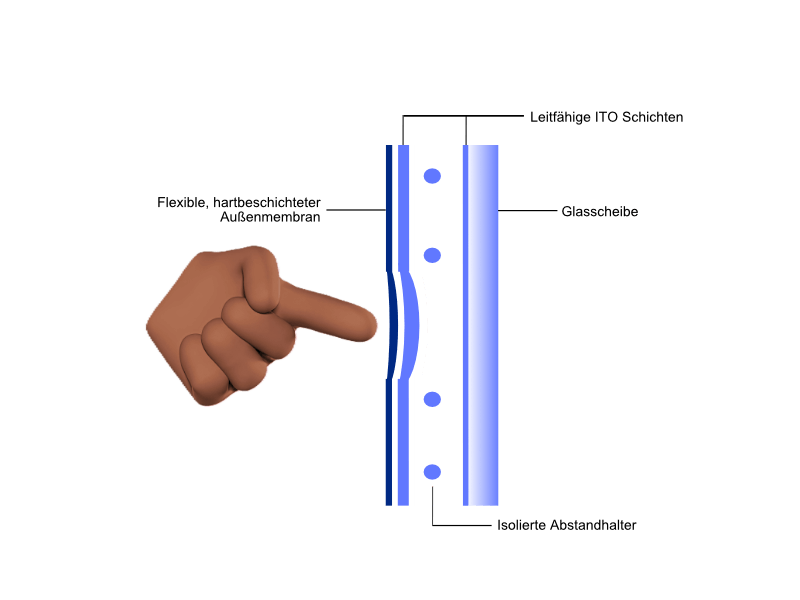
Resistive touch 4W and 5W
A further distinction is made between 4W and 5W resistive touchscreens. 4W are 4-wire resistive touchscreens. Each of the two layers has a printed conductive track on two opposite edges. In one of the two layers, the traces are on the top and bottom edges, and in the other layer, they are on the left and right edges. The built-in control unit applies a DC voltage to one of the layers. The positive pole is connected to one track and the negative pole to the other. The magnitude of the resulting voltage flow depends on how close to the positive or negative busbar it is read. On contact, the voltage layer comes into contact with the voltage probe (counter layer). The controller then measures the voltage at the contact point and can use this data to find the contact point (either X or Y) in the layer. To obtain the second layer, the controller switches functions (X instead of Y or vice versa). This switching occurs more than 100 times per second to ensure a fast response time without delay.
In 5-wire touchscreens, the conductor track is only on the lower layer for voltage measurement, not on both layers as in 4-wire technology. The upper layer is used only as a voltage probe to measure the voltage of the lower layer. As with the 4-wire, the controller measures the voltage on one layer and transmits it to the other layer. With the 5-wire probe, the voltage is only transmitted to the lower layer. It has a special conductor pattern that allows the switching function in one layer.
WEROCK uses only 5W touchscreens for all products, as the single-layer lower conductive layer means that micro-damage to the upper layer cannot affect performance and accuracy.
Surface Acoustic Wave Touch: The sensitive one
Surface Acoustic Wave touch, or SAW touch for short, is not triggered by pressure like resistive touchscreens, but by touch like capacitive touchscreens. Unlike PCAP touch, SAW touch is much more sensitive and can be operated with a finger or soft stylus. It is based on ultrasonic wave touch detection technology and the desire for almost complete light transmission.
Consisting of a glass panel with two transmitting and two receiving transducers and sound wave reflectors around the edges, the Acoustic Wave Touch detects touch without any noticeable delay. The emitting transducers generate ultrasonic waves that propagate across the entire surface of the panel. When a finger or soft stylus touches the touch surface, a portion of the wave is absorbed. The resulting change in the ultrasonic wave detects the exact position and sends the information to the controller for processing. The glass thickness can also be increased or up to three layers of glass can be used using an ion exchange process.
This rather exotic technology is used in public information kiosks in airports, train stations, and museums. Other applications include terminals in banks or ticket vending machines in indoor areas. Advantages and disadvantages of touch technologies
Due to the different structure of touch screen technologies, the possible applications also differ. The following sections explain the advantages and disadvantages of each technology.
Pros and cons of each touchscreen
Pros and Cons of PCAP Touch
The PCAP touch offers a number of advantages. A key feature is the multi-touch operation made possible by the transparent sensor. A screen can be touched with up to ten fingers simultaneously. Unfortunately, operation with gloves is not possible. Only bare fingers or very thin conductive gloves can operate the projective capacitive touch. On the other hand, the touchscreen scores with a very long service life, as the user interface still works even after scratches or knocks. It is also waterproof, easier to clean, and more resistant to chemicals and dirt than other touch technologies. These advantages are also reflected in the price, as PCAP touch is more expensive than other technologies.
The Projective Capacitive Touch is ideal for outdoor use. Its high transparency, visibility, and ruggedness allow it to withstand any harsh environment. Multitouch enables easy operation and advanced features.
Pros and Cons of Resistive Touch
Compared to capacitive touch, the resistive touchscreen can only be operated by touching it once. On the other hand, the printing technology scores points when it comes to operation. No conductivity is required and therefore allows operation even with thick gloves or non-conductive input pens. One disadvantage of this technology is the high level of wear and tear and the ever decreasing market share. This is due to improvements in PCAP touchscreens in the area of resistivity. The resistive surface is usually sensitive due to the very thin top layer. Capacitive touchscreens have the advantage that scratch-resistant and thick glass panels can be used, which significantly improves durability. Nevertheless, resistive touch is versatile and offers an attractive advantage over other technologies due to its low manufacturing costs.
True to the motto “old but still gold”, resistive technology continues to be a winner in all work scenarios where gloves or similar are used.
Advantages and Disadvantages of the SAW-Touch
Surface Acoustic Wave Touch, the third touchscreen technology introduced, was designed for maximum light transmission and detailed graphics. It should be noted that this technology no longer has a large market share and has been increasingly displaced by the emergence and improvements of PCAP touch. The trend for SAW touch continues to decline. The only argument for the continued use of this technology is the fact that wave touch is less susceptible to manipulation. There are many other points against it. First, it is generally only single-touch, not multi-touch, and is in the mid-to-high price range. Secondly, dirt, dust, water droplets and other influences can affect the user interface.
They are not recommended for rugged applications, especially outdoors, due to various characteristics (environmental degradation, single touch, etc.).
Improved strength and color with optical bonding
Optical Bonding improves the optical and mechanical properties of any touchscreen. Optical Bonding is a special bonding technique that uses an adhesive (OCR = liquid, transparent adhesive or OCA = solid, transparent adhesive) to bond the touchscreen to the LCD. There should be no air gap between the two layers.
The benefits of this technology include improved touch performance, reduced reflections, and improved readability in bright sunlight. In addition, the display is sealed against dust and dirt particles by sealing the layers. This provides increased durability and robustness.
WEROCK offers the option of optical bonding for all Rocksmart Panel PCs so that all displays can be used optimally in harsh environments. This is already included in our Scoria handhelds.
Conclusion: The Right Choice for Every Application
It is important to know for which application scenario I need a solution. New interactive digital signage is needed in shopping malls. They need to be easy to use, have high brightness, and increase durability. Both resistive and capacitive touchscreens are possible solutions. People in the construction industry often work in harsh environments with varying environmental influences such as light conditions or weather changes. Rugged, durable outdoor displays that can be used with gloves are required. Resistive touchscreens are more in demand for this application scenario. The capacitive touchscreen becomes attractive again for medical personnel and for operation with thin gloves and bare fingers. These are just a few scenarios where the problem, the environmental criteria and the possibilities must be taken into account.
No matter what application you need a display for, we can help you find the best solution. Click HERE to contact us today!